Danielle Tan
Chief Operating Officer
The ISO 14064-1 standard provides guidelines for organizations to quantify, monitor, and report greenhouse gas emissions and removals. This aims to explain the purpose and scope of ISO 14064-1, helping readers understand its importance in greenhouse gas reporting and environmental management.
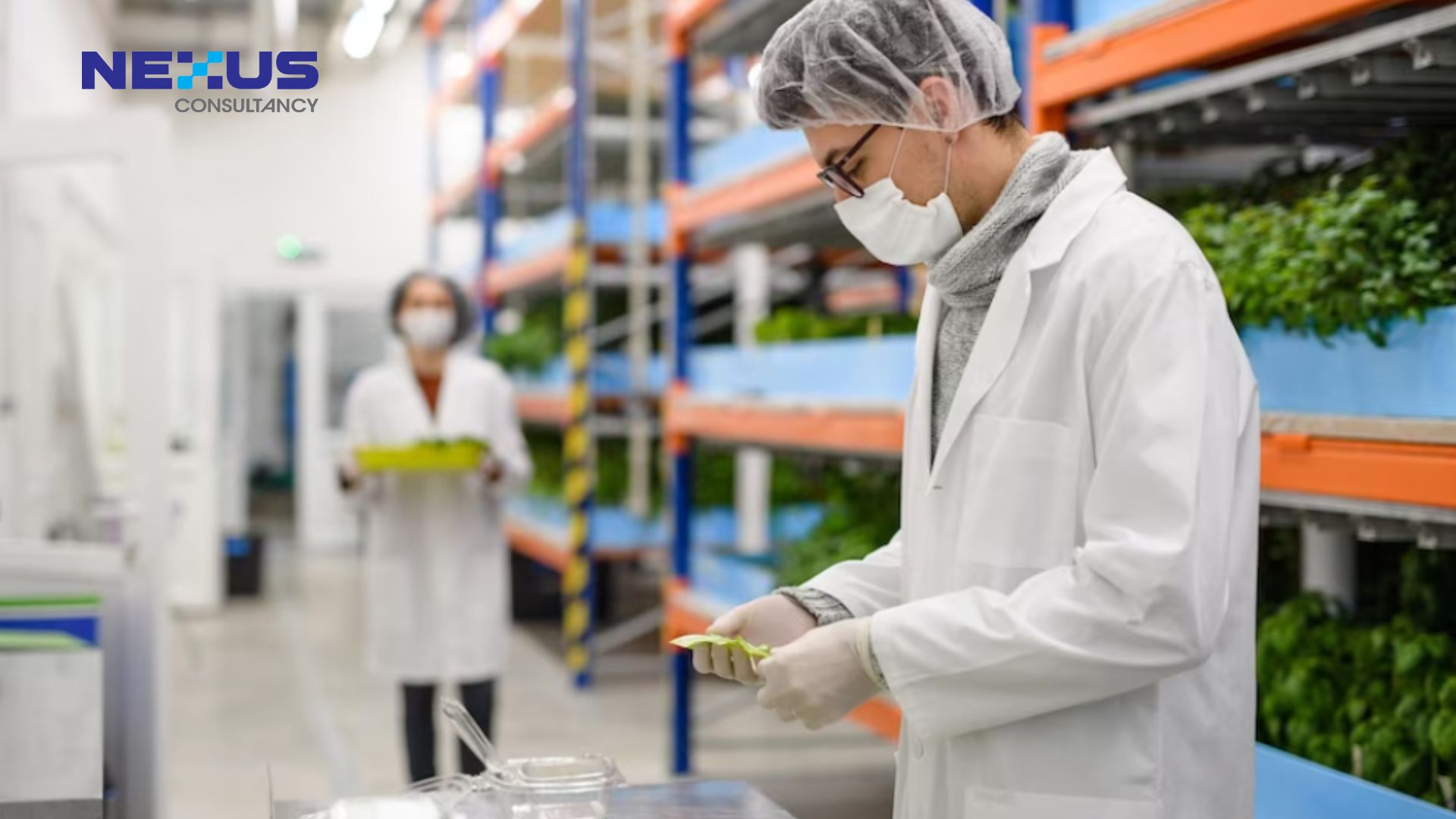
In recent times, the term “food safety culture” has become commonplace. However, for many individuals, understanding how this concept translates into their daily activities remains unclear. The essence of the term lies in its fundamental elegance – encapsulating the actions of employees from the moment they step into the facility to when they depart. Essentially, food safety culture reflects a company’s stance on food safety and the attitudes of its workforce.
Participating in any Global Food Safety Initiative (GFSI) audit such as FSSC 22000 Version 6 entails an assessment of your company’s “food safety culture,” even if not explicitly stated in the scheme requirements. Auditors scrutinize staff interviews, training programs, and production observations to evaluate the dedication to producing safe food. Whether your company deals with agricultural products, raw materials, or finished goods, the employees’ culture profoundly influences the safety and quality of your products.
Management’s role is pivotal in shaping food safety culture, emphasizing the need for a top-down approach. This is evident in all GFSI audit schemes, which incorporate a “management commitment” section. Food safety culture extends beyond Good Manufacturing Practices (GMP) compliance; it reflects the company’s trajectory.
Proving a strong food safety culture involves several key elements” communication, training, employee feedback and engagement and performance measurement. In this article, we are going to talk about guidance on auditing the communication element.
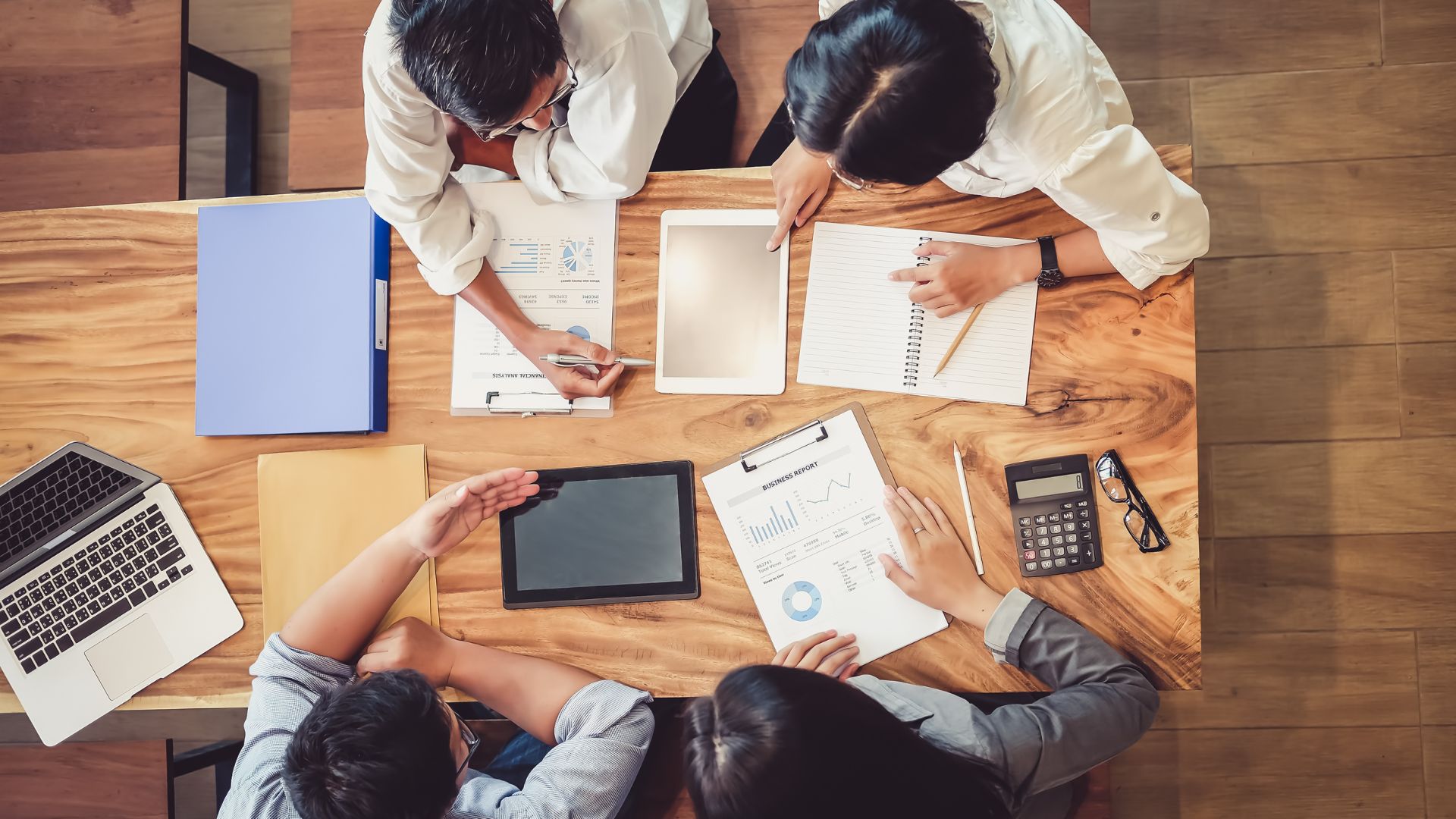
Guidance on Auditing the Communication Element
1. Senior management can demonstrate their engagement with food safety by establishing expectations for every department and throughout the organization with regard to food safety and quality culture e.g. establish whether this is included within job descriptions.
2. Verify how food safety and quality culture aspects are communicated throughout the organization e.g. establish if the organization has a communication policy and communication matrix.
3. Verify how top management has verified that all staff e.g. understand food safety and quality culture expectations, verify whether this is included within induction and annual training for personnel, and whether it included an assessment of personnel’s understanding.
4. Interview personnel on the shop floor to determine whether employees know their responsibilities and what they are accountable for in relation to food safety and quality-related tasks. Verify how personnel receive feedback on production performance and food safety/ quality issues e.g. verify if there are weekly or monthly production meetings and include feedback on production performance and food safety/ quality issues.
5. Assess during interviews with top management whether they can explain the organization’s food safety and quality expectations and how they are used in the decision-making processes.
6. Assess during interviews with the shop floor to which level personnel are informed on food safety and quality expectations. E.g. check the level of comfort and ease with which the auditee explains or responds when asked about the expectations, such as whether they know what to do when a nonconformance occurs. Can they describe for their section/ area of work what nonconformance is?
7. Assess the capability of top management to react to, e.g. customer complaints or supplier issues, in a timely and effective manner whilst ensuring the right decisions are made. This can be assessed during the interview with top management as well as when sampling customer complaints and corrective actions.
8. Assess whether food safety and quality-related expectations are communicated in a language understood by the personnel on the shop floor. E.g. look out for examples of translated materials either posted on the walls where employees work or other areas such as canteen walls.
9. Verify the training material is available and translations are in the local language and sample and examine answer sheets if written tests are used for verification of competence.
GFSI Guiding Question
- How do your senior leaders engage with food safety?
- How is your messaging used to communicate food safety expectations to all employees?
- Is your company’s vision and mission clearly expressed so that all staff understands both?
- Are you confident that all employees know their responsibilities and are held accountable for their food safety-related tasks and that accountabilities are well-connected?
- Can you articulate your company’s food safety expectations and how they are applied to every decision?
- Does your strategy enable you to respond quickly and effectively, with appropriate oversight, to ensure the right decisions are made?
- Can you identify examples of where using industry intelligence has helped identify potential hazards or risks to your business?
Conclusion
To sum it up, “food safety culture” is a vital aspect of how a company operates. It’s not just a trendy phrase—it’s about how employees act every day, impacting the safety and quality of products. In GFSI audits like FSSC 22000 Version 6, the focus is on how committed a company is to food safety. Communication, training, feedback, and performance measurement are key elements. The article provides practical tips for auditing the communication part, ensuring everyone in the company understands and follows food safety expectations. Following these practices is crucial for success in the ever-evolving world of food safety.
Take the First Step Towards Excellence! Contact us today to learn more about how your organization can elevate your food safety standards and establish a culture of excellence within your organization.